1. Automation of Processes
One of the most effective ways to boost quality and productivity in pharmaceutical manufacturing is to automate as many processes as possible. Automation eliminates the need for manual labor, reducing the risk of errors and improving efficiency.
It also enables the use of advanced technologies, such as sensors and machine learning algorithms, which can collect and analyze data in real-time to continuously optimize processes. Automated systems can also reduce the time required for routine tasks, freeing up valuable resources for more complex and value-adding tasks.
2. Implementing Lean Manufacturing Techniques
Lean manufacturing is a set of principles and practices designed to eliminate waste and streamline processes. By adopting these techniques, pharmaceutical manufacturers can reduce production costs, improve quality, and increase productivity.
Some of the key elements of lean manufacturing include standardizing processes, reducing inventory levels, and optimizing production flows. Implementing lean manufacturing techniques can also lead to increased innovation, as it frees up resources and encourages the development of new and better ways of doing things.
3. Implementing Quality Management Systems
Quality management systems are designed to ensure that products are manufactured to the highest standards and meet regulatory requirements. By implementing a quality management system, pharmaceutical manufacturers can improve quality and productivity by reducing the number of errors and rework.
This can be achieved through the use of tools such as process controls, statistical process controls, and continuous improvement programs. Quality management systems can also help ensure that processes are standardized and that all employees are trained on the best practices for their roles. Find A comprehensive GMP audit checklist | Pharmaceutical Firms
4. Investing in Research and Development
Research and development is a critical component of the pharmaceutical manufacturing process. By investing in R&D, manufacturers can continuously improve processes, develop new and better products, and stay ahead of the competition. R&D also enables manufacturers to identify and address quality and productivity issues before they become major problems, improving overall efficiency and reducing costs.
5. Collaborating with Suppliers
Collaboration with suppliers is another important factor in increasing quality and productivity in pharmaceutical manufacturing. By working closely with suppliers, manufacturers can ensure that the products and materials used in the production process are of the highest quality and meet regulatory requirements.
This can also help reduce costs, as manufacturers can negotiate better prices and receive products in a timely manner. Collaboration with suppliers can also lead to the development of new and better products, as suppliers can provide valuable insights into the needs of the market and the latest trends in the industry.
6. Investing in Employee Training and Development
Investing in employee training and development is another key factor in increasing quality and productivity in pharmaceutical manufacturing. By training employees on the latest technologies, best practices, and regulatory requirements, manufacturers can ensure that their workforce is equipped to meet the challenges of the industry. Employee training and development can also lead to increased engagement and motivation, which can improve overall performance and productivity.
7. Adopting Quality by Design (QbD) Approaches
Quality by Design (QbD) is a systematic approach to product and process design that focuses on the quality of the final product. By adopting QbD approaches, pharmaceutical manufacturers can ensure that their processes are designed and optimized for quality, reducing the risk of errors and increasing productivity. This can be achieved through the use of tools such as risk assessment, process characterization, and design of experiments.
8. Utilizing Real-Time Monitoring and Data Analytics
Real-time monitoring and data analytics can provide valuable insights into the performance of pharmaceutical manufacturing processes. By collecting and analyzing data in real-time, manufacturers can identify areas for improvement and optimize processes to increase quality and productivity. This can be achieved through the use of sensors, machine learning algorithms, and real-time data visualization tools.
9. Implementing Continuous Improvement Programs
Continuous improvement programs are designed to continuously improve processes and products over time. By implementing these programs, pharmaceutical manufacturers can ensure that their processes are always improving and that their products are of the highest quality. This can be achieved through the use of tools such as root cause analysis, problem-solving teams, and continuous process improvement programs.
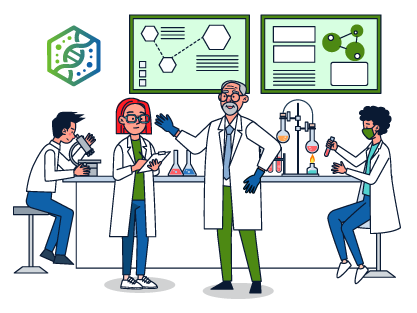
How GxPorbit helps Pharmaceutical Firms with GMP Audit Service?
GxPorbit’s GMP Audit Service can significantly boost quality and productivity in pharmaceutical manufacturing by providing a comprehensive assessment of a company’s Good Manufacturing Practices (GMP) compliance. By conducting a GMP audit, GxPorbit can identify areas for improvement and provide recommendations for enhancing quality and productivity in pharmaceutical manufacturing.
The GMP Audit Service offered by GxPorbit involves a thorough review of a company’s quality management systems, processes, and procedures to ensure that they comply with GMP regulations. This includes a review of documentation, facilities, equipment, and personnel training. During the audit, GxPorbit’s team of experts evaluates the company’s compliance with GMP requirements and identifies any potential non-conformances or areas for improvement.
The GMP Audit Report provides a comprehensive summary of the GMP Audit, including an assessment of the company’s GMP compliance and a detailed analysis of any identified non-conformances or areas for improvement. This report is a valuable tool for pharmaceutical firms to use to optimize their processes and improve their GMP compliance.
The GMP Audit Checklist covers all aspects of quality management and is used to evaluate a company’s compliance with GMP requirements. This includes evaluating documentation, facilities, equipment, and personnel training. During the GMP Audit, GxPorbit’s qualified and highly experienced consultants assess the company’s GMP compliance and identify any potential non-conformances or areas for improvement.
By identifying areas for improvement and providing recommendations, GxPorbit’s GMP Audit Service helps companies to increase quality and productivity in pharmaceutical manufacturing. This is achieved by reducing the risk of errors, improving process efficiency, and ensuring that products are of the highest quality. In addition, the GMP Audit Service also helps companies to meet regulatory requirements, which can increase their competitiveness in the market.
Conclusion:
There are many innovative ways to increase quality and productivity in pharmaceutical manufacturing. By automating processes, implementing lean manufacturing techniques, investing in R&D, collaborating with suppliers, and investing in employee training and development, manufacturers can stay ahead of the competition and remain competitive in today’s fast-paced and ever-evolving industry.
Top 10 Benefits of GMP Audits for Pharmaceutical Firms
Introduction Good Manufacturing Practices (GMP) are a set of guidelines and regulations that ensure the safety, quality, and consistency of...
Improving Compliance: Supplier Qualification in GMP Audit
Introduction: One crucial component of the GMP audit checklist is supplier qualification, which ensures that suppliers are providing materials that...
Ensuring GMP Compliance: Top 10 GMP Audit Checklist Items
Introduction: GMP audit checklists are an essentials in ensuring compliance with Good Manufacturing Practice (GMP) regulations in the pharmaceutical...
Maximizing Product Quality and Compliance through GMP Audit
What is a GMP audit? A GMP audit is a comprehensive assessment of a pharmaceutical, biotech, or medical device company's facilities, processes, and...
Best GMP Audit Services for Pharmaceutical Industry | GxPorbit
What is a GMP Audit? A GMP audit, short for Good Manufacturing Practice audit, is a comprehensive evaluation of a pharmaceutical company's processes...
How to Conduct a GMP Audit: Techniques and Best Practices
Good Manufacturing Practice (GMP) refers to the guidelines and standards established by regulatory agencies such as the Food and Drug Administration...
A comprehensive GMP audit checklist | Pharmaceutical Firms
What is GMP? GMP, or Good Manufacturing Practice, refers to the regulations set forth by regulatory agencies such as the FDA (in the United States)...
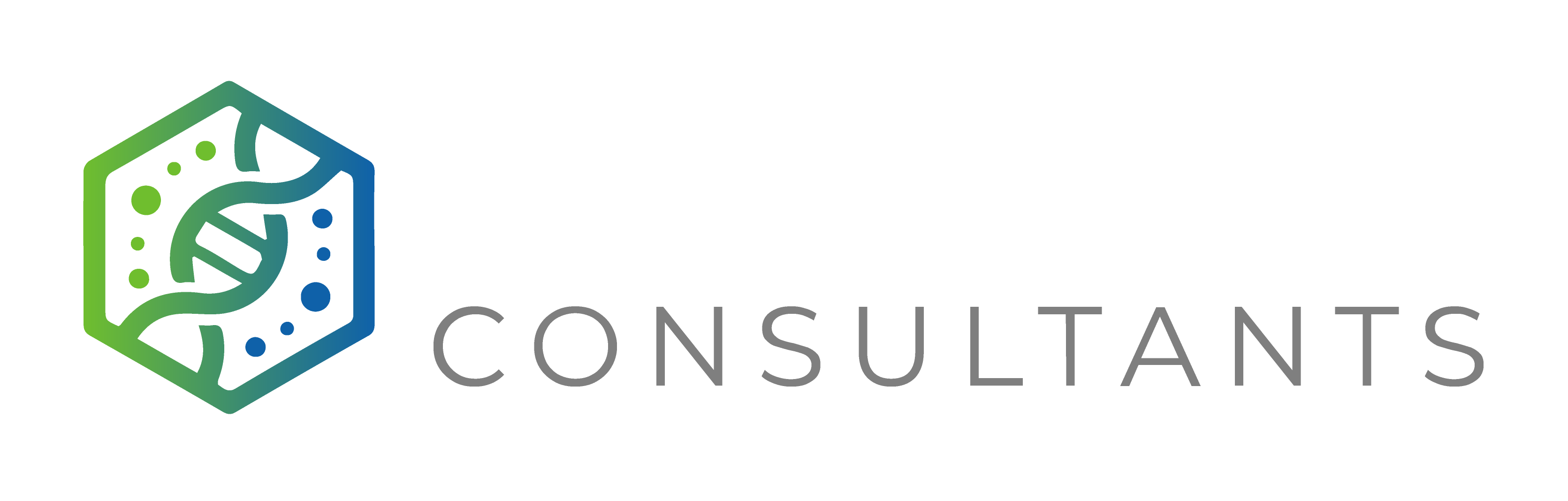
Office Address
No 182, Zhaohui Road, Hangzhou 310014, China
No 139, Mayuri Nagar, Hyderabad 500049, India
Quick Services