Good Manufacturing Practice (GMP) refers to the guidelines and standards established by regulatory agencies such as the Food and Drug Administration (FDA) for the production and quality control of pharmaceuticals, biologics, and medical devices. GMP standards are designed to ensure that these products are manufactured consistently and meet the required quality standards.
GMP auditing is an important part of the GMP compliance process. It involves an independent, systematic, and documented assessment of a company’s facilities, processes, and systems to determine if they are in compliance with GMP standards. This helps companies identify areas for improvement, ensure the quality of their products, and maintain the confidence of regulatory agencies and the public in their products.
The purpose of this article is to provide a comprehensive overview of the GMP auditing process and best practices. The article will cover the key aspects of GMP auditing, including preparation, conducting the audit, corrective action, report preparation, and follow-up. By following these best practices, companies can ensure that their GMP auditing process is effective, efficient, and in compliance with GMP standards.
Preparation for GMP Audit
A. Assemble the Audit Team
The first step in conducting a GMP audit is to assemble a team of qualified individuals who have the necessary skills and expertise to carry out the audit. The team should include individuals from various departments within the company, including quality assurance, production, and regulatory affairs.
The team leader should be a senior quality assurance professional with extensive experience in GMP auditing. Other team members should have relevant technical expertise and knowledge of the specific products and processes being audited.
Each team member should have a clearly defined role and responsibility during the audit. The team leader is responsible for overall management and coordination of the audit, while other team members may focus on specific areas such as product testing, process control, or documentation.
B. Define the Audit Scope
The next step in preparing for a GMP audit is to define the scope of the audit. This involves determining which facilities, products, and processes will be included in the audit. The scope should be defined in a way that ensures that all relevant aspects of the GMP compliance program are covered.
C. Establish Audit Objectives
Once the scope of the audit has been defined, the next step is to establish clear and specific audit objectives. This involves determining the specific goals of the audit and what needs to be achieved. The objectives should be aligned with the overall goals of the company’s GMP compliance program and should be based on the most critical risks facing the company.
D. Develop an Audit Plan
Once the audit objectives have been established, the next step is to develop an audit plan. This involves creating a detailed plan for conducting the audit, including the timeline, resources, and personnel required. The audit plan should be reviewed and approved by senior management to ensure that it is feasible and aligned with the overall goals of the GMP compliance program.
E. Create an Audit Checklist
An audit checklist is a critical part for conducting a GMP audit. It should be comprehensive and cover all relevant aspects of GMP compliance, including facilities, products, processes, and documentation. The checklist should be reviewed and approved by senior management and should be used as a guide during the audit to ensure that all relevant areas are covered.
Conducting the GMP Audit
A. Document Review
The first step in conducting a GMP audit is to review relevant documentation, such as Standard Operating Procedures (SOPs) and batch records. This involves evaluating the documentation to ensure that it meets GMP standards and that all critical processes are adequately described and controlled. The document review should be thorough and systematic, and any deviations from GMP standards should be noted as potential non-conformances.
B. Site Inspection
The next step in conducting a GMP audit is to physically inspect the facility. This involves evaluating the physical layout, equipment, materials, and overall appearance of the facility to ensure that it meets GMP standards. The site inspection should be thorough and systematic, and any deviations from GMP standards should be noted as potential non-conformances.
C. Interviews with Personnel
Interviews with personnel are an important part of the GMP audit process. This involves speaking with individuals from various departments within the company, including quality assurance, production, and regulatory affairs, to gain a better understanding of the company’s GMP compliance program. The interviews should be structured and systematic, and should focus on key areas such as product testing, process control, and documentation.
D. Identification of Non-conformances
The final step in conducting a GMP audit is to identify deviations from GMP standards and record them as non-conformances. This involves reviewing all of the information gathered during the audit, including the document review, site inspection, and personnel interviews, and identifying areas where GMP standards are not being met. The non-conformances should be documented in a comprehensive and systematic manner, and should be reviewed and approved by senior management. Also read 9 Ways to Boost Quality, Productivity in Pharma Manufacturing
Corrective Action Request (CAR) Process
A. Explanation of the process for creating a CAR and the importance of documenting it
After the GMP audit is complete, a Corrective Action Request (CAR) is created to document any non-conformances identified during the audit. The CAR process involves documenting the non-conformances in a systematic manner and assigning responsibility for correcting each issue. The CAR should be reviewed and approved by senior management, and should include a timeline for completion. The importance of documenting the CAR lies in the fact that it provides a clear and concise record of the non-conformances, the steps taken to correct them, and the results of those corrective actions.
B. Explanation of the steps involved in following up on corrective actions
Once the CAR is approved, the next step is to follow up on the corrective actions. This involves monitoring the progress of the corrective actions and ensuring that they are completed within the specified timeline. The follow-up process should be systematic and comprehensive, and should include regular updates and status reports. The objective of the follow-up process is to ensure that all non-conformances are corrected in a timely and effective manner, and that the company remains in compliance with GMP standards.
Audit Report Preparation
A. Explanation of the process for compiling the findings of the audit into a report
The final step in the GMP auditing process is to compile the findings of the audit into a report. This involves organizing the data gathered during the audit, including the document review, site inspection, personnel interviews, and non-conformances, into a clear and concise report. The report should be well-structured and easy to understand, and should provide a comprehensive overview of the GMP compliance status of the company.
B. Explanation of the importance of including recommendations for improvement in the report
In addition to documenting the findings of the audit, it is also important to include recommendations for improvement in the report. These recommendations should be based on the data gathered during the audit, and should provide practical and actionable steps for improving GMP compliance.
The recommendations should be comprehensive, relevant, and easy to implement, and should be reviewed and approved by senior management. The importance of including recommendations for improvement lies in the fact that they provide a roadmap for continuous improvement and ensure that the company remains in compliance with GMP standards. Get 3rd Party GMP Audit Compliance Services in China, India
Follow-up on Corrective Actions
A. Importance of Following Up on Corrective Actions
- Ensuring that non-conformances are addressed effectively: The follow-up process is crucial in ensuring that the corrective actions taken to address non-conformances are effective and resolve the underlying issues.
- Preventing recurrence of non-conformances: By verifying that corrective actions are effective, organizations can prevent the recurrence of non-conformances and maintain GMP compliance over time.
- Demonstrating ongoing commitment to GMP compliance: By following up on corrective actions, organizations demonstrate their commitment to GMP compliance and their dedication to maintaining high standards.
B. Process for Verifying the Effectiveness of Corrective Actions
- Review of updated documentation: This involves reviewing updated SOPs, batch records, and other relevant documentation to verify that they reflect the corrective actions taken.
- Re-inspection of the facility to verify changes: This involves physically inspecting the facility to verify that changes made as part of the corrective action process are in place.
- Interviews with personnel to verify understanding of changes: This involves conducting interviews with personnel to verify that they understand the changes made and are following the updated procedures.
- Review of performance metrics to assess the impact of corrective actions: This involves reviewing performance metrics such as product quality and production efficiency to determine if the corrective actions have had a positive impact. Read 9 Ways to Boost Quality, Productivity in Pharma Manufacturing
- Comparison of current status with the initial findings: This involves comparing the current status of the facility and its processes with the initial findings of the audit to determine if the corrective actions have been effectively implemented.
It’s important to note that the follow-up process should be documented, and the results should be documented and shared with relevant stakeholders to demonstrate the organization’s ongoing commitment to GMP compliance. Additionally, the follow-up process should be repeated regularly to ensure ongoing GMP compliance.
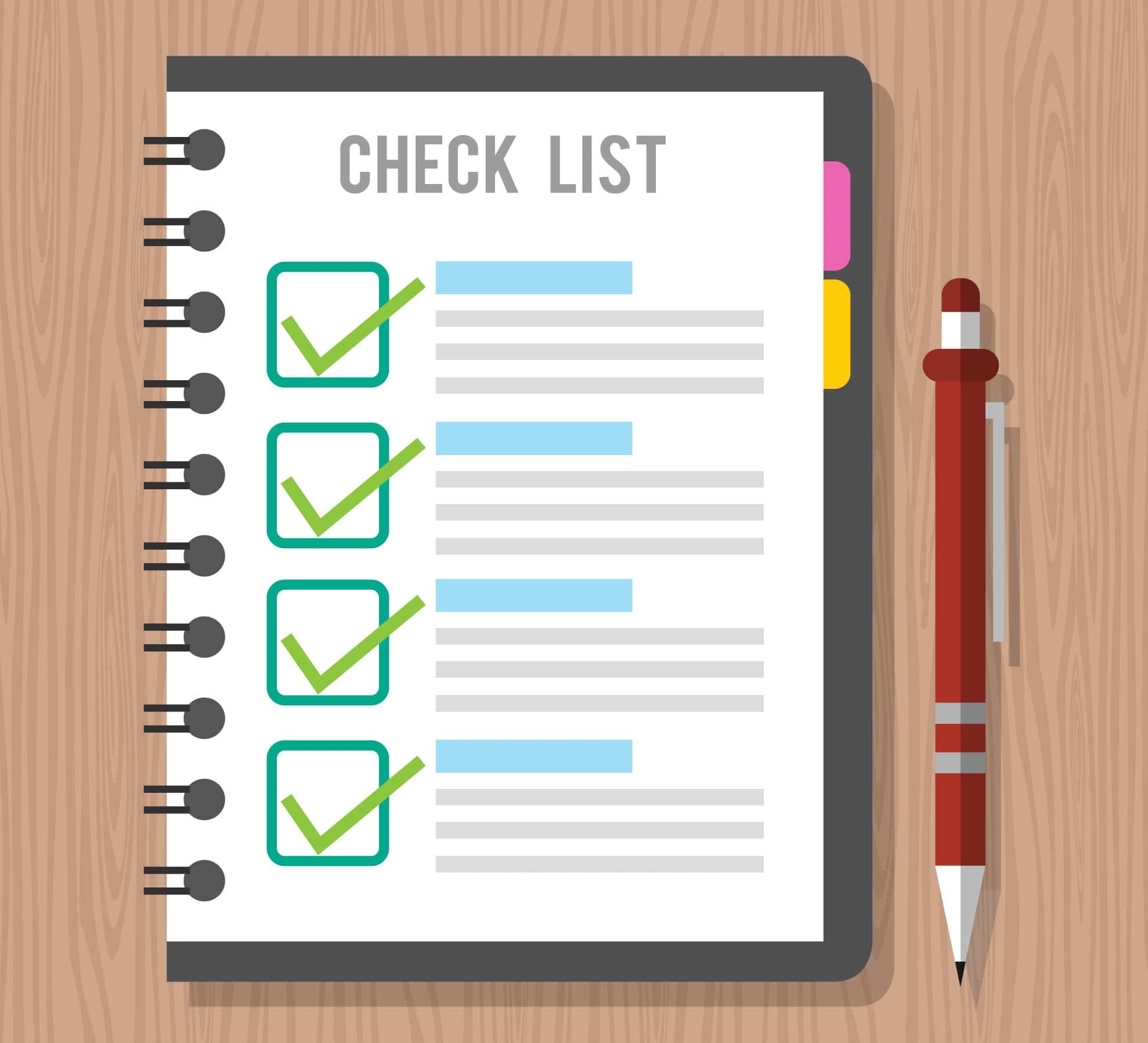
What is the golden rule of GMP?
The golden rule of GMP (Good Manufacturing Practice) is to ensure that every step in the manufacturing process of a pharmaceutical product is performed with the goal of producing a safe and effective product. This means following strict guidelines for facility design and maintenance, personnel training, equipment and process validation, product testing, and record keeping.
The golden rule of GMP also requires continuous monitoring and improvement of the manufacturing process to ensure that the highest quality standards are being maintained. The ultimate goal of following the golden rule of GMP is to protect patients by ensuring that they receive safe and effective products and to maintain public confidence in the pharmaceutical industry.
GMP Audit Checklist for the Pharmaceutical Industry
GMP, or Good Manufacturing Practice, is a critical aspect of the pharmaceutical industry. It involves a set of standards and guidelines that ensure the quality and safety of pharmaceutical products.
A GMP audit is an essential part for ensuring that these standards are being met. This GMP audit checklist for the pharmaceutical industry is designed to help you ensure that your operations are in compliance with GMP standards.
GxPorbit provides of GMP audit consulting services for the pharmaceutical industry. With extensive experience and a team of highly qualified GMP audit consultants, GxPorbit is well-equipped to help pharmaceutical firms prepare for a GMP audit.
One of the key areas where GxPorbit can provide assistance is in the preparation phase of the GMP audit process. This phase is critical to the success of the audit and includes assembling the audit team, defining the audit scope, establishing audit objectives, developing an audit plan, and creating an audit checklist. GxPorbit’s experienced consultants can provide expert guidance and tips to ensure that each of these steps is completed effectively and efficiently.
In addition, GxPorbit offers a comprehensive range of GMP audit services to help pharmaceutical firms prepare for a GMP audit. This includes a GMP audit checklist, which is designed to ensure that all relevant areas of the facility are inspected, as well as an audit report template that can be customized to meet the specific needs of each company.
GxPorbit also provides training and education services to help companies understand the GMP audit process and best practices, as well as ongoing support and guidance to help companies maintain compliance with GMP standards. With GxPorbit’s support, pharmaceutical firms can be confident that they are well-prepared for a GMP audit and can achieve the best possible outcome.
Find Services offerd by GxPorbit
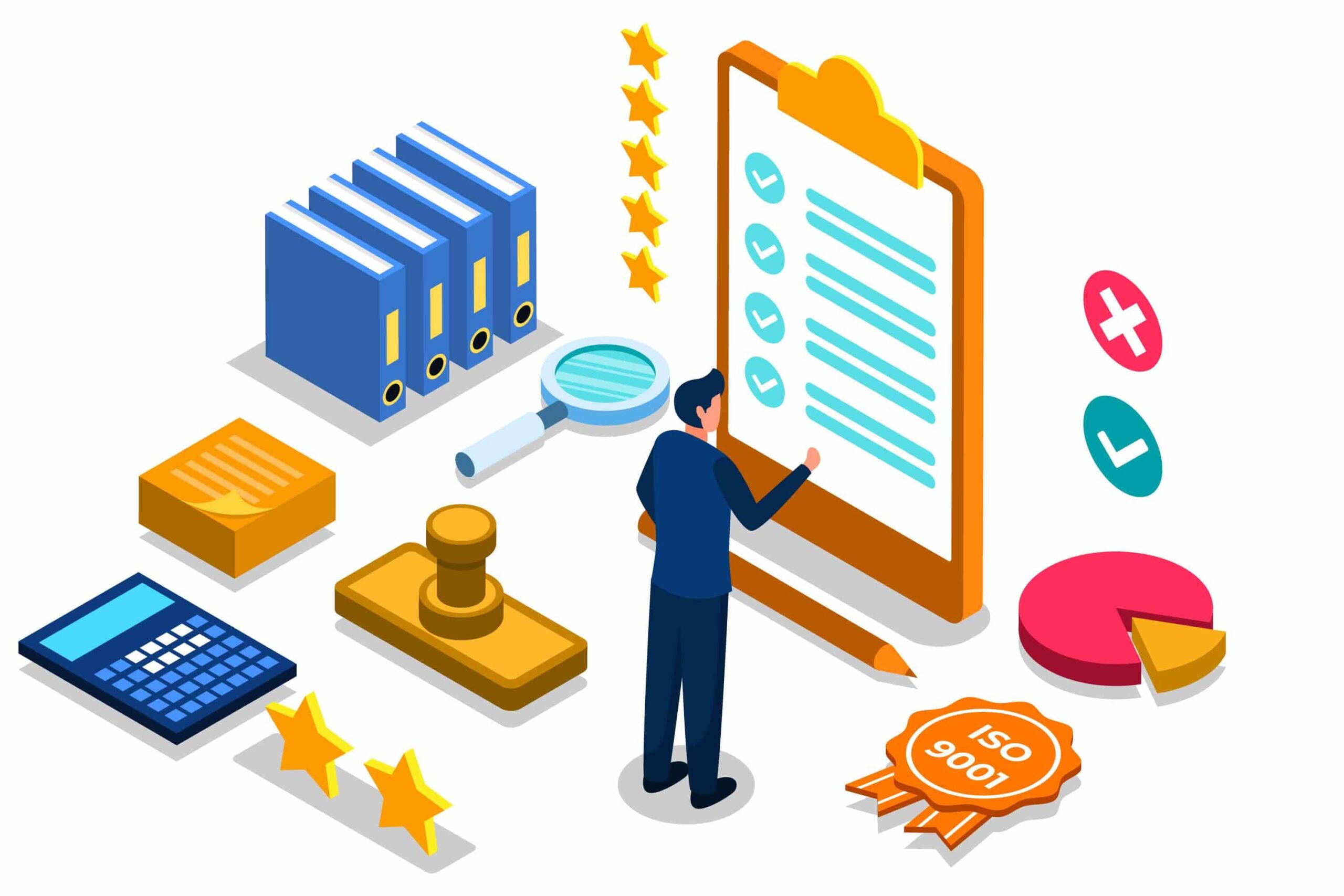
Conclusion:
GMP auditing is a critical component of ensuring that pharmaceutical companies meet regulatory requirements and produce safe, high-quality products. A well-conducted GMP audit can identify areas of non-compliance and provide opportunities for improvement to ensure continued compliance with GMP standards.
The GMP auditing process involves a comprehensive preparation phase that includes assembling the audit team, defining the audit scope, establishing audit objectives, developing an audit plan, and creating an audit checklist. During the actual audit, the team conducts document review, site inspection, personnel interviews, and identifies non-conformances. These non-conformances are documented through the Corrective Action Request (CAR) process and addressed through follow-up. The findings of the audit are compiled into an audit report, which includes recommendations for improvement.
It is important to follow up on corrective actions to verify that they have been effectively implemented. This can be done through monitoring and tracking, as well as conducting periodic re-audits to assess continued compliance with GMP standards.
By following best practices for GMP auditing and implementing effective corrective actions, pharmaceutical companies can ensure that their products are of the highest quality and meet regulatory requirements. Regular GMP audit is core objective for ensuring continued compliance and maintaining the trust of consumers.
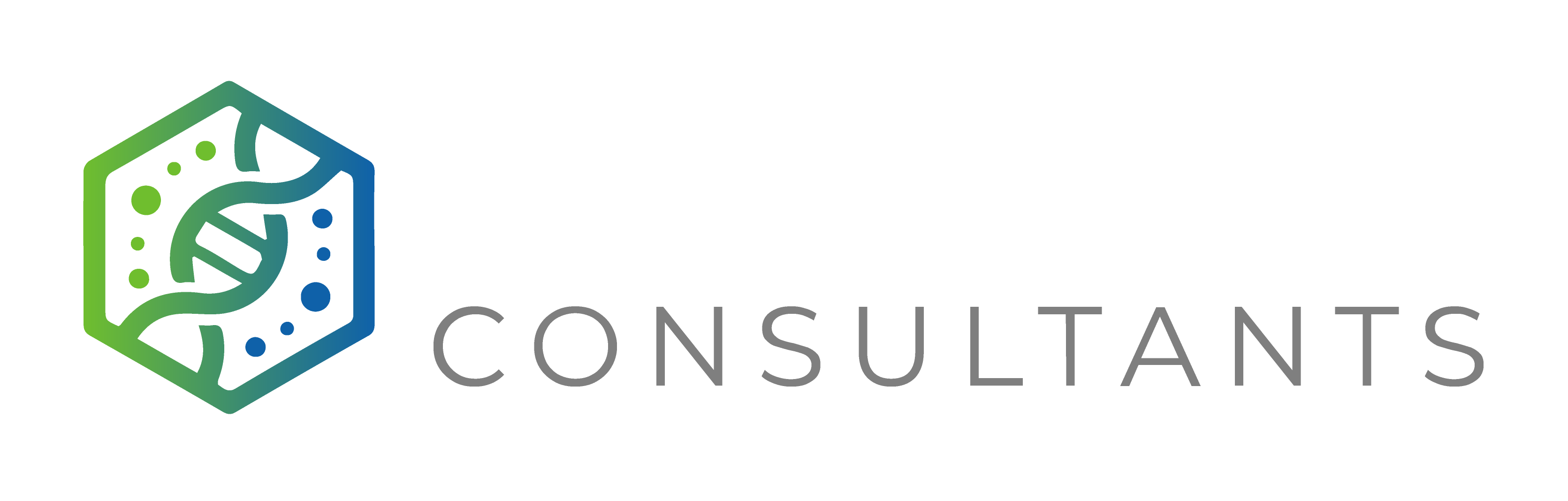
Office Address
No 182, Zhaohui Road, Hangzhou 310014, China
No 139, Mayuri Nagar, Hyderabad 500049, India
Quick Services